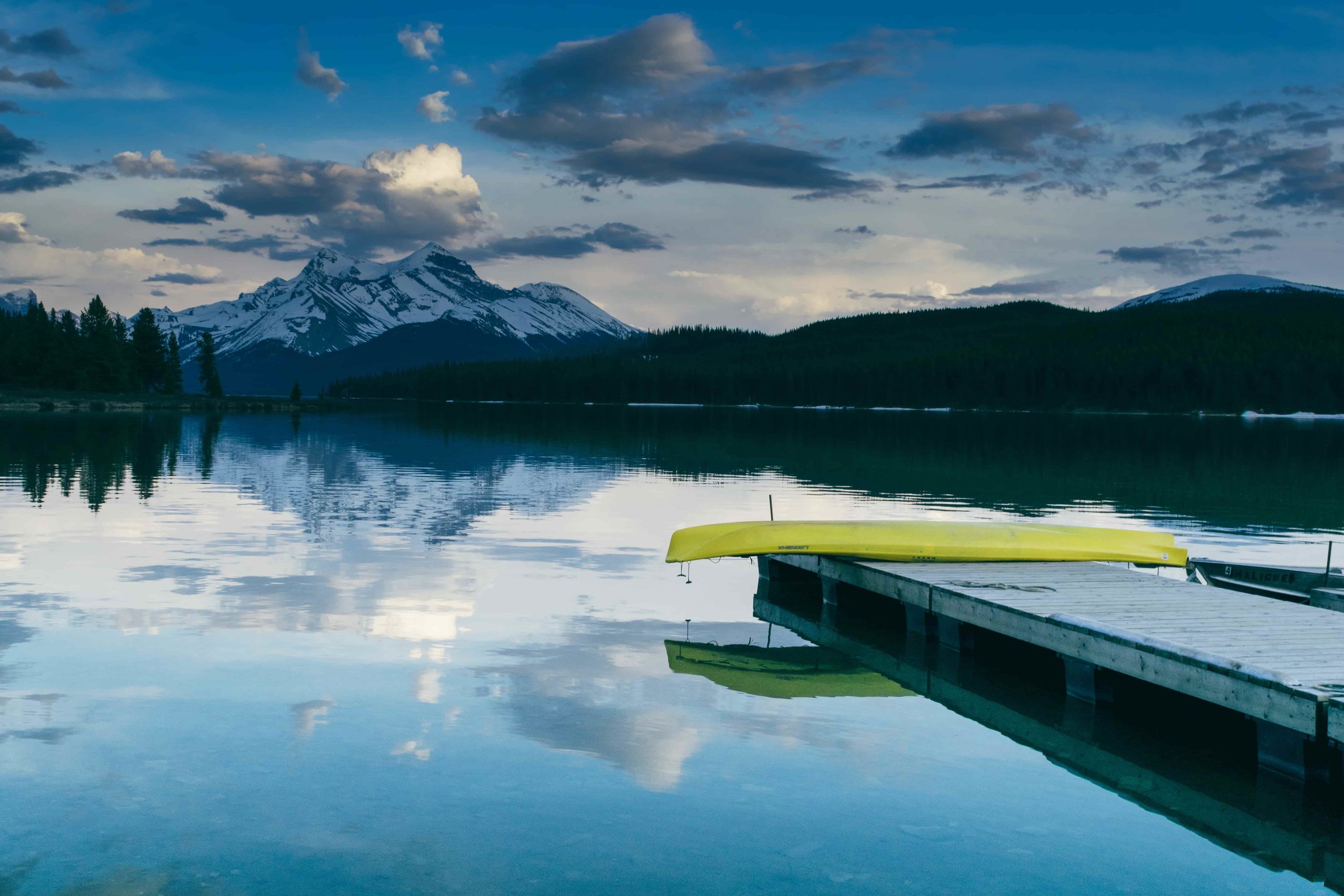
THE SUPPLY CHAIN BLOG
An Introduction to Voice Directed Picking (VDP)
Voice picking technology is equipment that allows for hands-free and eyes-free capability in the warehouse. It is currently becoming a new standard in distribution centers, used primarily for outbound operations but can be applied to any process in a warehouse. This is because for outbound operations, voice-directed picking (VDP) increases overall productivity, accuracy, and safety in the facility.
What is Voice Picking?
Voice picking technology is equipment that allows for hands-free and eyes-free capability in the warehouse. It is currently becoming a new standard in distribution centers, used primarily for outbound operations but can be applied to any process in a warehouse. This is because for outbound operations, voice-directed picking (VDP) increases overall productivity, accuracy, and safety in the facility.
VDP adapts Bluetooth technology and integrates with the warehouse’s WMS or ERP system. Rather than an employee reading information off a picklist or scanner, the system communicates to the employee via a wireless headset and directs them where to go in the warehouse and what to pick. VDP also provides real-time confirmation, removing the need of physical scanning and the logging of information, thus improving efficiency.
What are the Benefits?
Reduce Mis-Picks and Increase Safety
As mentioned, VDP creates a hands-free environment. It removes the need to press buttons, manually log/interpret information, etc. Instead, the employee on the headset follows instruction from voice commands and audio feedback which is directly logged into the WMS system. This can reduce the number of mis-picks that would normally be caused by human error due the ease-of-use VDP provides.
Safety in the warehouse is the most important element in any facility. There are many factors to consider such as material handling equipment and other employees on the floor which can cause unwanted accidents. VDP’s capability allows employees to be more aware of their surroundings when traveling around the warehouse. They are no longer distracted from reading their pick list or scanner throughout the warehouse and only have to focus on traveling safely to their pick location.
Increased Productivity
According to Körber Supply Chain, integrating VDP in the warehouse will usually create a 20-25% increase in productivity. The integration immediately eliminates the need for extra paper and hand-held devices which decreases the time to stop, read and scan items and picklists. Instead, listening and speaking allows for the user to multitask during the picking procedure. Then, as data is collected over time, even more productivity can be found by finding the most optimal pick-route. This information can be extracted to decrease travel time within the warehouse. These increases in productivity reduces the labor needed for picking which allows reallocation of resources where needed.
VDP is also seen being integrated with picking robots to further increase productivity. In addition to an employee utilizing VDP, picking robots will utilize the average pick and travel time to ensure that the picker and robot are just-in-time with one another. These robots provide an additive feature in the automation process.
Data and Continuous Improvement
This method not only provides real-time information but simultaneously collects data to provide helpful statistics such as how long the task will take to complete and average number of items on the pick list. These statistics are important for continuous improvement in the warehouse. Access to this information ensures that the pickers are arrived on time, at the correct location, and on a larger scale, maintain KPIs.
The Future of VDP
As warehouses continue to introduce new technology, the use of VDP will continue to grow as it increases accuracy without the sacrifice in time. Integration with picking robots will most likely grow in parallel due to their complimentary functionality, further increasing standards. The freedom that VDP allows a company to address other bottlenecks in the warehouse such as quality assurance or inventory storage by reallocated picking labor to where needed. Not only will productivity increase in the warehouse, but VDP also provides an avenue for companies to become more data-driven, which is critical for continuous growth and improvement.
Digital Twin Technology - From Concept to Reality
Digital twins are the next step in the evolution of simulation technology. Early developments began in the 21st-century, starting from computer-driven simulations to the creation of AutoCAD and other simulation applications that have grown to current system design programs. Technology such as increased computing power and reliable sensors has made digital twins a real possibility.
Digital twins are the next step in the evolution of simulation technology. Early developments began in the 21st-century, starting from computer-driven simulations to the creation of AutoCAD and other simulation applications that have grown to current system design programs. Technology such as increased computing power and reliable sensors has made digital twins a real possibility.
What exactly are digital twins?
The digital twin is a solution to help bridge the physical and digital world. Digital twins take 3D modeling to the next level by capturing more than just static information and becoming a live e-model of the product. Sensors capture dynamic data that provides the accurate state of the product to better support areas such as prevention, troubleshooting, and quality management. It provides feasible and realistic simulations that will or could happen with a product. To put into simpler terms as defined by IBM, “The digital twin is the virtual representation of a physical object or system across its life-cycle. It uses real-time data and other sources to enable learning, reasoning, and dynamically recalibrating for improved decision making.”
The common key characteristics of a digital twin given by DHL are:
1. A digital twin simulates both the physical state and behavior of the thing
2. A digital twin is unique, associated with a single, specific instance of the thing
3. A digital twin is connected to the thing, updating itself in response to known changes to the thing’s state, condition, or context
4. A digital twin provides value through visualizations, analysis, prediction, or optimization
Effects in the Supply-Chain and Logistics Industry
Digital twins in the early stages were being used in high-value and high-criticality products such as aerospace and defense. Now, companies are starting to collect data for the use of digital twins outside of these industries. This can create a major influence in the product life cycle and manufacturing.
Product life cycle
· Faster design iterations
· Reduced development costs due to decrease in physical prototypes
· Competitive advantage in fast-tracking a product into the market
· Increased reliability of final product
Manufacturing:
· Distinct specifications for suppliers, creating optimized shipping and manufacturing designs
· Models with specific components and materials for all products
· Conduct realistic simulations for layouts, processes, and material flow before facility is created
· Troubleshoot product faults to help find root causes and optimize future performance
Challenges
The biggest challenge that digital twins face in the logistics industry is the quality of data. Current digital twins are not exact e-replicas of the product. This is because it is extremely expensive to collect and clean data such as the physical, chemical, electrical, and thermal state of a product. To bypass this, engineers are using assumptions and simplifying their models.
Collecting high-quality data can be expensive which poses the question if implementing digital twins are worth it. High-value and high-criticality industries will continue to expand digital twins, but we may not see adoption in the commercial industry in the near future.
Ensuring a Successful Supply Chain Network Optimization Study
We previously wrote about some of the reasons and incentives for why a company would want to execute a supply chain network optimization study. Now, we would like to discuss some of the key contributing factors to consider when completing the supply chain network optimization study that will ensure both realistic and usable results.
We previously wrote about some of the reasons and incentives for why a company would want to execute a supply chain network optimization study. Now, we would like to discuss some of the key contributing factors to consider when completing the supply chain network optimization study that will ensure both realistic and usable results.
Modeling Tools
A supply chain network optimization study cannot be completed without using a supply chain modeling software tool. Modeling tools will be able to handle all the necessary data and backend calculations so that the user can focus on having the right inputs and interpreting the outputs. There are many different tools out there that will get the job done and each one has different pros and cons. Some of the main ones today include Supply Chain Guru, Blue Yonder and AIMMS, as well as our internal proprietary tool, ASSIGN.
Data
We talked about the multitude of data analysis that will be delivered during a supply chain network optimization study, but data will also be the major input that drives the model and strategy development. That being said, it is important to spend a large amount of the time up front focusing on the data. Collecting the right data and making sure the data is of reliable quality will determine how complex and detailed the study can get. The most important data to look at includes transportation/shipment data, sales order history data and inventory data. Getting all the supply chain cost elements (in particular, warehousing costs) will also be important for establishing the baseline costs. Because the data being used will be very granular, validating the data against financial reports is another extremely important step to ensure the data driving the project is correct and the project’s results, are therefore, realistic.
Business Rules & Constraints
While data is the most important factor during a supply chain network optimization study, the business rules and constraints should not be overlooked. This will be what restricts the model and ensures that the results are optimized to support the goals of the business. Business rules and constraints refer to parameters like a min or max inventory on hand and order fulfillment time (e.g. customers receive goods within 4 days) and should be discussed in the beginning of the project and updated as necessary. With the right software tool, these can be put right into the model.
Forecasting and Planning Factors
When reviewing the results of the supply chain network optimization study, it is important that they not only will work for the business as things are today but also will support the business over the next 5 years and beyond. That is why it is important to consider the demand forecast (as detailed or generic as it may be) and any planning factors. Planning factors are things that won’t be seen in the data, but should be considered, and can be anything from the opening/closing facility to tariff increases to needing a distribution center to be within a certain distance of a specific location. Ensuring that the forecast is properly understood, and all the planning factors are laid out early in the project, will be vital to feasibility of the results at the end of the project.
Considerations When Designing a Warehouse
Whether you are opening a new warehouse or distribution center, adding a product line, exploring automation, or just running out of space, there are many different considerations when optimizing a warehouse layout and associated processes. We wanted to share some insight regarding the Establish methodology for warehouse design projects, specifically the inputs we like to gather before any concepts are drawn or recommendations made.
Whether you are opening a new warehouse or distribution center, adding a product line, exploring automation, or just running out of space, there are many different considerations when optimizing a warehouse layout and associated processes. We wanted to share some insight regarding the Establish methodology for warehouse design projects, specifically the inputs we like to gather before any concepts are drawn or recommendations made.
First Steps – High Level Planning
The beginning of a warehouse design project should include a few conversations – those that define the scope of the project, success metrics, key stakeholders, and any headaches or concerns that should be solved by the new layout. It is important to lay everything out on the table, because the ‘optimal’ layout is not always the best suited to the operation and employees involved. Before beginning the project, it is paramount to understand company values, value propositions, goals, sales channels, customers, seasonality, and forecast. Additionally, involving all affected employees or group representatives and establishing rapport keeps everyone’s interests aligned.
Process & Material Flows
Following a high-level understanding of the business, the warehouse processes are of highest priority in determining warehouse layout. There is no better way to learn about process than physically being on the warehouse floor, walking through each decision point step-by-step. Shadowing, documenting, and talking with operators will be your greatest resources – no one knows the process better than those working it day-in and day-out. The time with operators develops buy-in for the future layout, ensuring that everyone’s needs and challenges are considered. While shadowing, it is important to remember to follow the entire lifecycle of a product through the warehouse, from the time it enters the premises through delivery into the customer’s hands. We’ve found that having a thorough understanding for the operation leads to better data analysis later in the project.
Data Analysis on Volumes
In addition to the qualitative observation of process, warehouse design should include a healthy amount of quantitative data analysis to determine product volumes and order profile as these are what dictate labor and spatial requirements. Order profile is the single most important piece of data for warehouse design, it is the driver for process and storage. Understanding how product is ordered, be it pallets/cases/eaches, will define what picking strategies you can deploy (think pick by order, batch, cluster, wave, or zone picking). Having a grasp on peak volumes, not just averages, assures the operation can withstand those high-volume days. Order profile, picking strategy, and volumes help determine inventory space necessary and labor hours involved.
Bringing it Together
The combination of process knowledge and data analysis as inputs for the design will allow for a better chance to land on a solution that is both optimal and meets the needs of the business. Once we’ve developed planning factors and worked through this qualitative and quantitative approach to the inputs, we can begin to iterate through concepts. Think of the observations and analysis we’ve done before as puzzle pieces – each piece (i.e. the amount of racking for a product, staging space, or machinery) is a defined amount of space. From here, we fit all those pieces together, draw material flows to follow the life cycle of the product, and visualize. After that, it’s all iteration.
What are the Benefits When Completing a Supply Chain Network Study?
It does not matter if a company is business-to-consumer (B2C), business-to-business (B2B) or direct-to-consumer (DTC), if the company distributes goods, then the supply chain will play a vital role. That being said, it is important for companies to be active when reviewing their supply chain network to ensure that it is set up optimally to support the business. We find that supply chain costs usually account for over 6-10% of sales, which can add up to a lot of money for large companies. Likewise, it is just as important for smaller companies to prioritize their supply chain strategy, as they may quickly and consistently outgrow or shift their current supply chain networks.
It does not matter if a company is business-to-consumer (B2C), business-to-business (B2B) or direct-to-consumer (DTC), if the company distributes goods, then the supply chain will play a vital role. That being said, it is important for companies to be active when reviewing their supply chain network to ensure that it is set up optimally to support the business. We find that supply chain costs usually account for over 6-10% of sales, which can add up to a lot of money for large companies. Likewise, it is just as important for smaller companies to prioritize their supply chain strategy, as they may quickly and consistently outgrow or shift their current supply chain networks.
One of the best ways to review the current supply chain strategy and determine how it can be improved is by doing a supply chain network study (aka supply chain network design or supply chain network optimization), which consists of loading data into a supply chain modeling software to test out different scenarios against the current supply chain (baseline). There are a lot of benefits that can come from doing a supply chain network study and some are more obvious than others.
Data Analysis
Every supply chain network study starts with lots and lots of data. This data will be used in more than one way throughout the study. In addition to being what drives the model, there are loads of analysis that take place in the beginning portion to understand the business and see what sort of inventory and distribution strategies make sense. We find that most of the time our clients do not have the time or resources to complete detailed analysis on a consistent basis so usually a lot is learned before the network modelling even starts. This can pinpoint areas for the company to focus on outside of the supply chain network study and lead to the development of different supply chain strategies that were not thought of previously.
The Baseline
Creating a digital replica of the current supply chain network costs, known as the baseline, is another major portion of the supply chain network study. This will show the current nodes or locations involved in the supply chain and all of the supply chain related costs. This information will give a good indication of where the highest costs are and be the starting point for comparing alternatives. In addition to costs, the baseline will also give a look into the current service levels being achieved, a visual representation of ship patterns, and a look at volumes vs capacity to see what areas of the supply chain might be strained.
Center of Gravity
The center of gravity analysis uses demand data to determine the optimal location or locations for a specified number of DCs. It can be a quick and simple way to answer questions about location and number of locations and will help make decisions when determining what scenarios to run later in the study.
Scenario Comparison
The ability to compare different scenarios without making any physical changes is probably the most significant deliverable when doing a supply chain network study. Once the baseline is created, different distribution strategies and node locations can be modeled to see their impact on costs, service levels, ship patterns and volumes against the baseline. Most scenarios tested should be based on the data analysis that was done, but there is a lot of freedom. If you have ever wondered what would happen if you moved your operation across the country or sourced products from the one country instead of another, a network study can tell you what that would look like.
The Final Deliverables
Supply chain network studies generate a lot of deliverables. The results/answers will be based on what is important to the business. Some companies might prioritize 2-day shipping where others want to minimize costs and improve bottom line. Regardless of the main goal, the supply chain network study offers insight into a variety of considerations, such as sourcing, distribution and inventory strategy including number of distribution centers, distribution center location(s), ship patterns and what to store where. This information can help make key strategic decisions for the supply chain and the business as a whole.
Self-Driving Trucks - A New Age for Ground Shipping
Self-driving commercial trucks have been a hot topic for the past few years as several companies have joined this sector in an innovative movement to become the first to establish a fully disengaged trucking network. A fully disengaged trucking network would negate the need for the driver to interact with the vehicle, but still be available in case of emergencies. The development of this technology could lead to possible reduced labor costs and reduced transit times.
Self-driving commercial trucks have been a hot topic for the past few years as several companies have joined this sector in an innovative movement to become the first to establish a fully disengaged trucking network. A fully disengaged trucking network would negate the need for the driver to interact with the vehicle, but still be available in case of emergencies. The development of this technology could lead to possible reduced labor costs and reduced transit times.
What are self-driving trucks?
Self-driving trucks or “robo-trucks” focuses on autonomous technology that does not require a human driver. The idea is like that of self-driving cars, but with constraints and considerations such as load weight and distance traveled. Though self-driving trucks and electric vehicles are commonly associated with one another, electric vehicles primarily focus on the renewable and sustainable energy mainly for the retail use. Though they are different, the two sectors have been developing almost in parallel.
Who are the major players and Where are we now?
A few major players in this area are Waymo, formally known as the Google self-driving car project, TuSimple, Gatik, and Embark. These companies have already began mapping out their trucking network and chances are you may have already seen them on the road. Waymo and GM Cruise have completed 11,017 and 5,205 miles respectively of disengaged travel. TuSimple’s longest mapped route is 1,000 miles between Phoenix and Dallas. In fact, they have begun a four-year plan to go nationwide by 2021, traveling cross-country from Los Angeles to Jacksonville. They also intend to completely remove a person behind the wheel is 2021.
Various partnerships have been established such as Waymo with UPS and AutoNation and the start-up Gatik will begin delivering for Walmart in 2021. Embark, in collaboration with Amazon, has begun transportation of Frigidaire refrigerators from El Paso to Palms Spring. Though we are far from implementing self-driving trucks on a nationwide scale, these partnerships represent the commitment to this sector.
Impacts and Looking Ahead
As self-driving trucks start to become more common, there are areas in supply-chain and logistics that will be affected and need to be considered.
1. Quality and Safety of goods
Who becomes responsible for the quality and safety of the goods? It could be placed upon the company to reformat their packaging strategy to be more secure or the freight forwarder to ensure that the transportation of goods is secured. The safety of the goods is a priority to consider which may impact the relationships and responsibilities between these entities.
2. Adaption of transportation management systems
As self-driving trucks become integrated in the industry, managers need to consider what new types of data need to be collected to ensure that the transportation of goods is optimal. When trucks arrive at their destination, how is communication going to be accurately logged and confirmed that the goods were not only obtained, but that the trucks are also meeting regulations? Transportation management systems will need to adapt to this new mode of transit and be able to consider new elements that may arise.
3. The career of truck drivers
A major discussion on the impact of self-driving is the career of truck drivers. With the male workforce dominating the trucking profession at over 90%, people wonder if it would make the career obsolete. Are these drivers expected to learn the new technology to keep up with the innovation? TuSimple has tried to proactively combat this possible problem by offering a program at Pima Community College to help truck drivers adapt to the new technology. On the other hand, self-driving trucks can be implemented as a driver assist technology (rather than driver replace) on long routes to reduce breaks required and travel time. For example, the 11-hour driving limit could be prolonged if the driver can rest while on route, reducing fatigue.
Circular Supply Chains - A Step Towards Sustainability
Building upon last week, we are taking a deeper dive into the sustainability movement of circular (a.k.a closed-loop) supply chain practices. The world is moving on from the 'cradle-to-grave' supply chain practice of product manufactured, distributed, used and thrown out. Circular supply chains can be described as the combination of standard logistics and reverse logistics in order to create a circular logistical lifecycle. Products in the reverse logistics flow can be redistributed, repaired for continued use, remanufactured in case of defects, or recycled into parts and materials that have been carefully selected for this purpose.
Building upon last week, we are taking a deeper dive into the sustainability movement of circular (a.k.a closed-loop) supply chain practices. The world is moving on from the 'cradle-to-grave' supply chain practice of product manufactured, distributed, used and thrown out. Circular supply chains can be described as the combination of standard logistics and reverse logistics in order to create a circular logistical lifecycle. Products in the reverse logistics flow can be redistributed, repaired for continued use, remanufactured in case of defects, or recycled into parts and materials that have been carefully selected for this purpose. This diagram maps out what a circular supply chain could look like:
Completely closing the loop is an incredibly ambitious goal - zero-waste is no simple task. Significant motivations for circular supply chain economics include the following:
1. Recovered product reduces waste, minimizes direct costs and offers secondary value. Waste reduction is clear - less product heads to landfills when its return is incentivized. Direct costs can be avoided by reusing product as input to production. Finally, secondary value is achieved through sale of recovered outputs on secondary markets.
2. Improved brand-image and customer loyalty. Circular supply chains, and sustainability in general, are mainstream - an outwardly sustainable company earns positive publicity. Returns, repairs, and refurbishment allow for consistent warranty practices that earn customer loyalty and future sales.
3. Product improvement through more data. With more products returning to producer's hands, the entire product lifecycle can be mapped out and defects, usage, and feedback can be utilized to improve product design.
Case Study: IKEA Furniture
In the last 10 years, patience as a consumer has become thin. 'Fast' trends are in - be it 2-day shipping, fast fashion, and even fast furniture. Similar to the way Zara and H&M turned the apparel industry into a race for who could adapt quickly and provide cheap trendy styles, the furniture industry has shifted towards products with a life cycle of 1-2 years. They are low-quality, easy to assemble, and can be left behind when moving residences. IKEA was at the forefront of this trend, and has made significant investment to shift their narrative and lead sustainability initiatives in the furniture industry.
IKEA has explored a multitude of strategies to push towards their goal to be 100% circular using only renewable and recycled materials. Their solutions range from product leasing to secondary markets to using circular materials that can be remanufactured into new products. While the company recognizes its shortcomings - and is realistically very far from their goal - these are big steps for an industry leader and Fortune 100 company to make. Read more about it here.
Why you Should Prioritize Reverse Logistics and Returns Management
This year, returns set an all new single-day high and certain companies are so overwhelmed that they are refunding consumers and telling them to keep the items rather than shipping them back. Returns have become a large pain point for many companies and can add a lot of extra costs when not handled correctly. A thorough understanding for reverse logistics and returns management can allow companies to minimize the added costs and recoup some value while earning increases in customer loyalty.
This year, returns set an all new single-day high and certain companies are so overwhelmed that they are refunding consumers and telling them to keep the items rather than shipping them back. Returns have become a large pain point for many companies and can add a lot of extra costs when not handled correctly. A thorough understanding for reverse logistics and returns management can allow companies to minimize the added costs and recoup some value while earning increases in customer loyalty.
Returns can happen in any industry for many different reasons. Whether the reason for return is the consumer’s fault (e.g. they ordered the wrong size), a carrier’s fault (e.g. product got damaged during transit) or the distributor’s fault (e.g. shipped an expired product) every company should prepare themselves to handle reverse logistics and returns.
The What: Standardized Process with Automated Workflows
All efficient returns management strategies rely on understanding returns data so that standardized processes can be built, and workflows can be automated. This will prepare an operation to handle all the different returns and minimize the decision making happening in real-time. Defining necessary functionality and selecting appropriate support systems is good practice. A pre-screen with the consumer to allocate the return into the correct workflow allows the logistics team to predict and plan for inbound goods. Workflows can vary company to company, but a quality check is consistent. Assessing goods and distribution into pre-determined workflows leads to quick turnaround time and fastest recouping of investment.
The Why: Financial Incentive AND Customer Loyalty
Financial incentive is clear – the opportunity to resell the goods and recoup value, whether on the primary market in full or a secondary market for fractions. What is less recognized, is the influence on customer management. Customer expectations are high for returns – quick and easy response with free shipping. Managing that relationship can go a long way. Remember that returns contribute to the bigger picture: customer loyalty and repeat sales.
The How: Valuation
With every product, being able to appraise a return is absolutely necessary. Understanding why the return is being made, any repair/refurbishment costs necessary and the future-value of the product reselling (if at all) on the primary or secondary market is key. Having a system in place to do so is extremely important. It has even led to some companies leaving the product with consumer free of charge.
Goods valuation does not paint the entire picture. A considerable piece of the puzzle is customer loyalty and retention. Determining value here is specific to each company, and something not to be ignored.
Looking Ahead
A trend significant of late is that of sustainability. Government regulations have taken interest in the proper disposal of goods and incentivized reuse and recycling. Secondary markets have flourished in recent years, leading to the development of closed-loop supply chains – those with 0 waste. We predict that 2021 continues to bring a focus to ESG initiatives, and that those not invested there will be left behind.